Nachdem die Laminier-Arbeiten beendet waren, blieb eine raue, recht unebene Oberfläche zurück. Einerseits verursacht durch die Faserstruktur des Glasfasergewebes, andererseits durch deutliche Vertiefungen und Wellen. Nun mussten wir uns etwas überlegen, um diese unebene Oberfläche glatt zu bekommen. Durch die runde Form des Rumpfes war zunächst unklar, wie wir die Unebenheiten erfassen und ausgleichen konnten. Unsere erste Idee zur Erfassung der Unebenheiten war die Abbildung des Urmodells als digitales 3D Modell. Damit hofften wir, genau erkennen zu können, an welchen Stellen vom Rumpf Unebenheiten ausgeglichen werden müssen. Mit Hilfe von Fotogrammetrie und CAD- Software sollte die dreidimensionale Form des Urmodells erstellt werden. Diese Idee scheiterte jedoch an der Umsetzung, denn es wären nicht nur viele Fotos hoher Auflösung sondern auch unzählige Arbeitsstunden am Rechner nötig gewesen um die Realität mit der nötigen Genauigkeit digital erfassen zu können. Nach einem Test, bei dem für ein kleines Rumpfsegment über 100 Arbeitsstunden nötig waren, wurde diese Idee endgültig wieder verworfen.
Also mussten wir uns eine neue Methode einfallen lassen. Nach Absprache mit dem Prüfer, der später das fertige Flugzeug abnehmen wird, fiel während eines Konstruktionstreffens die Entscheidung, die Verfeinerung der Oberfläche einfach mit Hand und Augenmaß durchzuführen. Die angewandte Technik basierte einheitlich auf fühlen, spachteln und schleifen.
Im ersten Schritt versuchten wir, die größeren Vertiefungen zu glätten. Zu deren Erkennung nutzten wir biegsame Latten. Wir legten sie auf das Rumpfmodell auf und konnten dann ohne Probleme die tiefsten Unebenheiten vermessen. Um möglichst wenig Spachtelmasse zu verbrauchen, spachtelten wir in zwei Gängen. Zuerst benutzten wir eine Zahnspachtel, die zwei Millimeter hohe, parallel angeordnete Wulste auf dem Modell hinterließ. Um die Riffelstruktur anschließend passend auf die Form des Rumpfes zu schleifen, benutzten wir ein langes, biegsames Stück Schaum. Im zweiten Gang füllten wir die Vertiefungen zwischen den Spachtellinien mit Spachtelmasse aus.
Der zweite Schritt verfeinerte die Technik, indem nun nicht mehr angezeichnet, gespachtelt und dann geschliffen wurde, sondern man die winzigen Unebenheiten ausschließlich mit der Hand erfühlte und danach spachtelte und verschliff. Das Spachteln erfolgte hier mit verdünntem Spachtel und einer geraden, biegsamen Plastikleiste, mit der der überschüssige Spachtel mit der Rumpfkrümmung abgezogen wurde. Überaschenderweise konnten wir mit dieser Methode jede noch so kleine Unebenheit, die mit dem bloßen Auge nicht mehr sichtbar war, erfühlen und ihrer Herr werden.
Die sukzessive Verfeinerung und Ausbesserung der Oberfläche wurde nicht nur mit zwei unterschiedlich feinen Methoden vorgenommen, sondern wir konzentrierten uns auch in zwei Schritten zuerst auf die horizontalen und dann auf die vertikalen Wellen und Unebenheiten.
Zum Schluss musste auch die Nase an das Rumpfmodell angepasst werden. Wir schnitten sie zuerst grob aus Styropor und verfeinerten sie dann ebenfalls mit Spachtel. Anfangs versuchten wir mit Orientierungsspanten und gedruckten Zeichnungen die perfekte Form zu finden, doch nachdem diese Techniken die Nase eher krummer als gerader machten, wurde auch hier mit sehen, tasten und fühlen die Form geschaffen. Im Ergebnis erhielten wir nun unser fertig verschliffenes Urmodell, dessen Oberfläche mit jeder investierten Arbeitsstunde besser wurde.
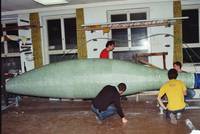
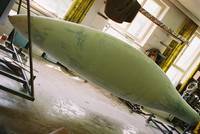
Comments are closed