Herausarbeiten des Übergangs zwischen Rumpf und Rumpfröhre
Nachdem die Schäftung erfolgreich durchgeführt war, gilt es also einen gleichmäßigen Übergang mit Spachtel herauszuarbeiten (1). Das gestaltet sich schwerer als gedacht. Zunächst wurde ein Übergang im CAD-Modell konstruiert und eine Form mit 6 Spanten in gleichmäßigem Abstand dafür gebaut. Wir hofften damit alle 20 cm den Übergang an die Spanten anpassen zu können und so Anhaltspunkte für das Spachteln des Übergangs zu gewinnen. Es sollte sich aber herausstellen, dass die Form für den realen Übergang nicht zu gebrauchen war. Durch zu große Abweichungen der Ist-Werte zum Soll der CAD-Daten wurde also dieser Übergang verworfen und beschlossen, die Kontur frei herauszuarbeiten. Mit Hilfe von viel Spachtel und langen Schleifleisten nähern wir uns also nun einer homogenen Form, die nicht mehr den CAD-Daten entspricht, aber dennoch eine gute Optik verspricht.
Um aus dem Flickenteppich zweier unterschiedlicher Spachtel und Kohlegewebe einen einfarbigen Untergrund zu schaffen, auf dem die letzten Unrundheiten besser erkannt und behoben werden können, wurde eine Schicht Füller auf die gesamte Röhre aufgebracht (2). Nachdem diese Schicht nun entsprechend behandelt wird, können die letzten verbleibenden unrunden Stellen noch einmal mit Spachtel ausgeglichen werden und erneut gefüllert werden.
Baubeginn der Hauptspantform
Parallel zu den Arbeiten am Rumpfübergang wurde mit der Herstellung der Form für den vorderen Hauptspant begonnen (3). Eine gewölbte Platte aus doppeltem Kohlegewebe mit Stützschaum dazwischen wurde zunächst vorbereitend geschliffen und gespachtelt, danach gefüllert und zuletzt die Oberfläche erneut fein geschliffen, um bald den ersten Spant davon abnehmen zu können. Die Form gibt hier nur die Wölbung des Spantes wieder, die Kontur muss nachträglich aus dem Spant herausgetrennt werden.
Vorbereitung der Stringer im Mockup
Ebenfalls parallel wird an der Herstellung von Glaskernen für den Haubenrahmen gearbeitet. Zunächst wird der Rahmen aus Schaumblöcken und Holz als Positivmodell in das Mockup geklebt. Danach können durchgehende Formen dieser Stringer abgenommen werden, in denen hohle Glaskerne hergestellt werden können. Diese hohlen Kerne können so direkt in der Form des Gesamtrumpfes in die Rumpfbelegung eingearbeitet werden und bilden den Haubenrahmen und gleichzeitig die tragenden Stringer im Cockpit.
Probleme bei der Herstellung der Positivmodelle sind die Unebenheiten in der Haubenkante des Mockups (4). Sobald die eigentliche Position der Haubenkante durch Messungen ermittelt wurde, werden die Kerne mit Hilfe von Holzplatten an ihre Position geklebt.
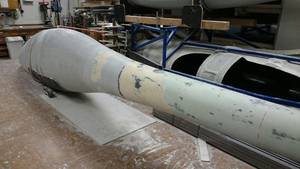
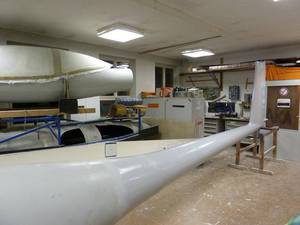
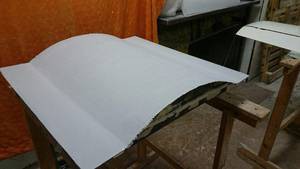
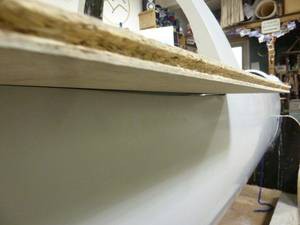
Comments are closed