Das erste komplett von mir übernommene Projekt an der Fertigung der D-B11 ist die innere Rumpfstruktur, welche aus den Berechnungen des Vorderrumpfes mit dem Augenmerk auf innovative Crashsicherheit.
Die Hauptschwierigkeit bestand in der genauen Herstellung der Geometrie, da die einzige lineare Projektion nicht ohne weiteres in das Rumpfmodell eingelegt werden konnte und keine verwendbaren, maßgenauen CAD-Modelle der Struktur vorhanden waren.
Der Spant besteht aus einem Kern aus Schaum, auf den mehrere Lagen Carbongewebe aufgelegt werden. Die dadurch entstandene Geometrie weist ein deutlich höheres Trägheitsmoment und Steifigkeit vor, ist also eine Verstärkung.
Ziel war es also eine Negativform herzustellen, in welcher man einen Schaumkern urformen kann. Eine Herausforderung dabei war, dass der Kern beim Entformen nicht zerstört werden konnte, wodurch die Form teilbar gestaltet werden musste.
Die Lösung lag im Einzeichnen des oberen und des unteren Punktes, an dem die Fläche, welche auf dem Spant liegt den Rumpf schneidet. An diese Stelle wird ein Styrodurblock eingelegt, welcher den gleichen Umriss wie der Spant hat. Dieser wurde hergestellt, indem ein Ausdruck vom Spantquerschnitt aufgeklebt wurde und die Kante abgeschnitten wurde. Dies geschah mit einem eigens dafür entwickelten Elektro-Carbon-Schneidegerät.
Nun wurde angedicktes Harz (ugs. Mumpe) in den Rumpf eingeschmiert, dabei hat der Kontakt des Styrodurblockes an den Rumpf die vordere Grenze gebildet.
Auf das Harz wurden zwei Lagen kleiner Hartschaumstücke (Conticell) Aufgelegt und mit angedicktem Harz verklebt. Die Schicht hatte dann die Dicke des Spanten und wurden auch auf die entsprechende Länge zugeschnitten.
Die durch diese Formgebung entstandene Geometrie war logischerweise fehlerhaft und wurde mit Gips zurechtgespachtelt, damit Breite stimmte und der Spant auf eine Ebene gelegt plan war.
Sobald die Geometrie des Kernes vollendet war wurde eine Phase aus Mumpe angebraucht. Diese wird in der Rechnung vernachlässigt, ist aber für eine Faserverbundgerechte Gestaltung ein wichtiger Punkt.
Der nächste Schritt bestand aus der Bearbeitung der Oberfläche. Hierfür wurde ca. 5 mal gespachtelt und geschliffen. Zuletzt wurde eine Schicht Formharz aufgetragen, damit bei bevorstehenden Entformungsvorgängen kein Harz abgelöst werden konnte.
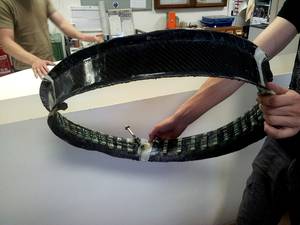
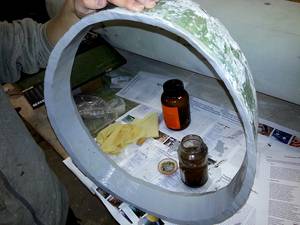
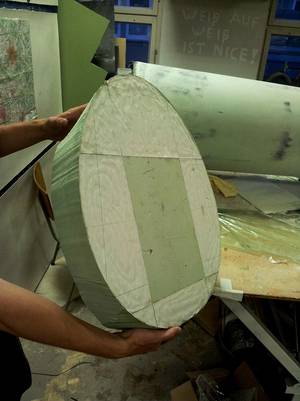
Comments are closed